A sandwich slab will impact your project!
Often, the appearance of a sandwich slab comes as a surprise on-site. The knock-on effects for an efficient scanning & coring process can be significant. We seem to be encountering more and more sandwich slabs on sites and they have presented some challenges.
What is a sandwich slab?
A sandwich or split-slab is a method of construction using two separate concrete slabs: the first is commonly a slab-on-grade or suspended "structural" slab covered with waterproofing and a drainage system; the second, or "topping" slab is placed over the underlying slab and waterproofing.
Since the 80s we've seen the addition of insulation between the slabs to protect the membrane from cracking at low temperatures. If the membrane cracks, then moisture can enter.
Where might you encounter one
Split-slab design is widely used in applications such as plaza decks (sometimes called podium decks); sports and assembly facility concourses and roadways, shopping malls and airport roadways.
The value of recognizing a sandwich slab
Recognizing sandwich slabs can be extremely difficult unless you have as-built drawings indicating the structural detail of the slab (which often don't exist) the slab looks the same as any other. Discovering one of these on-site can often lead to time delays, particularly when it comes to our contribution to a project - concrete scanning, and coring. Their presence can make the overall process much more complex and expensive.
Scanning these slabs also has its challenges. The presence of the layer of insulation does not help the scanning process as the radar's signal cannot penetrate this. So the scanning cannot be completed from the top-side alone. You will need to provide your scanning contractor with access to the underside of the slab to complete the process.
Once granted access to the underside of the structural slab, the crux of the problem comes down to the depth penetration of radar from the underside. If the structural slab can be successfully scanned from the underside, then the process is simple. Scan the topping slab, scan the underside of the structural slab, transfer these marks to the top side of the topping slab for engineer review.
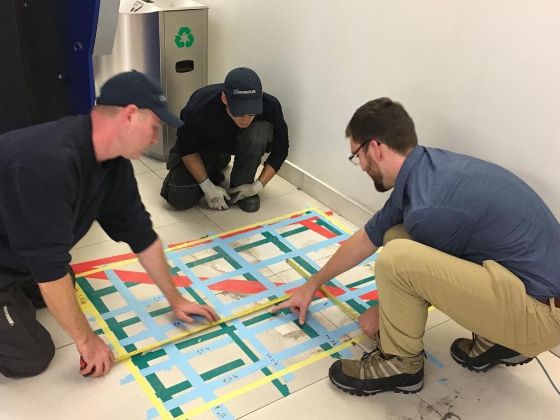
More often than not, successfully scanning the structural slab from the underside alone is not possible due to the thickness of the structural slab and/or density of steel within it. Often these slabs are very thick (14 - 28") and/or have dense steel at the bottom which affects the depth penetration of the radars signal.
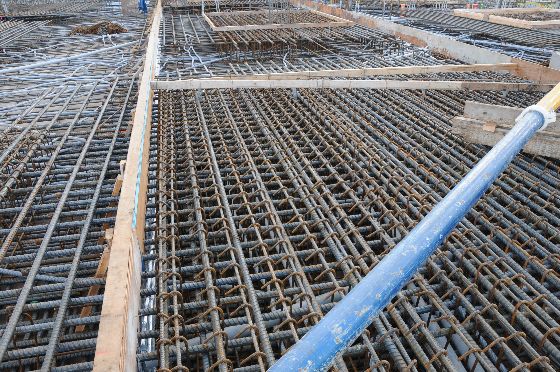
However, there is a solution but it can add potential unforeseen costs and time delays to your project.
Often the only course of action is to remove a portion of the topping slab and any insulation below it, to provide access to the structural slab to scan it from the top side. The ability to scan the structural slab from both sides often (but not always) means it can be scanned entirely, with marks from the underside transferred to the top for engineer review.
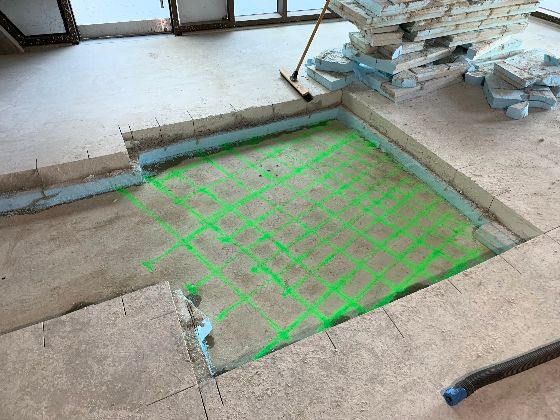
Another serious challenge posed by the overall thickness of these slabs (for example take a 5" topping slab with 4" insulation and a 24" structural slab) is how you spot where you are to the underside of the slab? Drilling pilot holes to locate where you are from below is not possible and transponders lose accuracy - up to ½ an inch over every 8 inches of thickness. "Spotting" is typically a straight-forward task on most slabs becomes a lot trickier and takes more time on these slabs.
Though tricky to deal with, successfully scanning and coring a sandwich-slab is not an insurmountable task. Having dealt with numerous large sandwich-slabs, we have figured out some approaches to save time you time and money.
Have you seen similar situations?
Give Xradar a call. We will work with you to figure out the best solution.